Steps to Having a Garage Built
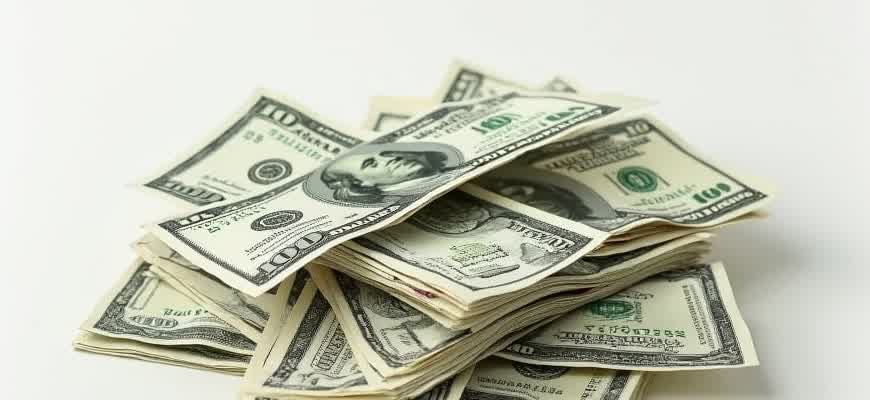
Building a custom garage involves careful planning and execution. To ensure a smooth process, several critical steps must be followed. The first step is to assess your needs and plan the design. Here’s a breakdown of how to proceed:
- Initial Planning: Determine the garage size, layout, and purpose (storage, parking, workshop, etc.). This will guide all future decisions.
- Check Local Regulations: Research zoning laws, permits, and building codes in your area. Ensure your garage complies with local standards.
- Budgeting: Estimate the costs for materials, labor, and any additional features like electricity or insulation.
Important: Contact your local planning office to confirm required permits. Failing to do so can delay the project and result in fines.
Once these initial steps are complete, proceed with the design and construction phases. Here’s a simple checklist of the following steps:
- Foundation preparation
- Frame and structure assembly
- Roof installation
- Exterior finishing
- Interior work and utilities
Step | Description |
---|---|
Foundation | Excavate the site and pour a concrete slab or build a foundation based on your garage’s needs. |
Framing | Construct the frame, including walls and roof supports. |
Roofing | Install the roof structure and cover it with weather-resistant materials. |
Define the Dimensions and Structure of Your New Garage
Before starting the construction of a new garage, it's crucial to decide on the size and overall design. The size should accommodate not only your current needs but also provide some flexibility for future requirements. A small garage may suffice for a single car, but if you plan to use it for storage, a larger space will be necessary. Consider factors such as vehicle size, extra storage space, and possible workshop areas.
Think about how you intend to use the garage and what type of layout will make it functional. The garage's interior should be organized and spacious enough to store both vehicles and other items without feeling cramped. Plan for door placements, workbenches, shelves, and even possible future installations such as charging stations for electric vehicles.
Key Considerations for Garage Size and Layout
- Number of vehicles to be stored.
- Amount of additional storage space required.
- Need for a workbench or additional workspace.
- Ease of access for vehicles and equipment.
- Space for potential future upgrades (e.g., electric vehicle charging ports, shelves).
Important: It’s a good idea to allow for extra space around your vehicles to ensure comfortable movement and ease of access.
How to Decide on Garage Size
- Single-Car Garage: A minimum of 12' x 20' (3.6m x 6m) is generally sufficient.
- Two-Car Garage: At least 20' x 20' (6m x 6m) is recommended for adequate space.
- Three-Car Garage: A common size is 30' x 20' (9m x 6m), providing ample room for vehicles and storage.
- Additional Space: Add around 4' to 6' (1.2m - 1.8m) to the length and width for extra storage or workspace.
Suggested Layout Features
Feature | Recommended Size |
---|---|
Workbench | 4' x 8' (1.2m x 2.4m) |
Storage Shelves | Varies, but at least 3' x 4' (0.9m x 1.2m) per section |
Vehicle Parking | 10' x 20' (3m x 6m) per car |
Research Local Zoning Laws and Building Permits
Before starting the construction of a garage, it is crucial to check your local zoning regulations and building permit requirements. Zoning laws govern land use in your area, and they define how your property can be utilized. These regulations can vary depending on the location and the type of construction you're planning. Understanding these rules ensures that your project remains compliant and avoids costly fines or delays.
Building permits are often required for any major construction project. These permits ensure that the structure meets safety standards and local codes. Failure to obtain the proper permits can result in the dismantling of the garage or legal penalties. Therefore, it's important to research and understand the permit application process early in your planning.
Steps to Research Zoning Laws and Building Permits
- Check with your local planning or zoning department to find out the specific zoning designation of your property.
- Look up the requirements for setbacks, height restrictions, and land use that may impact the size and location of your garage.
- Review local building codes to ensure your garage will meet structural and safety standards.
- Submit a formal request for a building permit, which may involve submitting site plans and construction drawings.
- Consult a local contractor or architect if you are unsure about the regulations or need help with the approval process.
Key Permit Considerations
Permit Type | Required Information |
---|---|
Building Permit | Blueprints, site plans, and structural details of the garage. |
Electrical Permit | If you plan to install electricity, wiring plans are needed. |
Plumbing Permit | Required if plumbing systems (e.g., a sink or drain) will be added. |
Note: Always ensure that the zoning laws for your area permit the type of construction you are planning. Some residential areas may have strict rules about the size and placement of structures.
Choosing the Right Foundation Type for Your Garage
When constructing a garage, selecting the proper foundation is crucial to ensure its longevity and stability. The foundation provides the base on which the entire structure rests, so it must be tailored to both the soil conditions and the design of the building. Whether you're building a small storage space or a large multi-car garage, the type of foundation you choose will directly affect its durability and functionality.
There are several foundation options available, and each one comes with its own advantages and considerations. Understanding the differences between them will help you make an informed decision based on your garage's requirements, local weather conditions, and budget.
Foundation Types to Consider
- Slab Foundation: Ideal for areas with stable soil, this option involves pouring a single, thick concrete slab. It's cost-effective and easy to install, making it a popular choice for smaller garages.
- Pier and Beam Foundation: This involves placing concrete piers or beams into the ground to support the structure. It is suitable for uneven or unstable soil and provides better ventilation under the garage.
- Full Basement Foundation: A more complex and expensive option, this foundation is perfect for larger garages or those intended to serve as workshops or additional storage spaces.
- Crawl Space Foundation: Similar to pier and beam but with a lower height. It provides space for utilities and ventilation while being less expensive than a full basement.
Key Considerations
- Soil Conditions: Before deciding on a foundation, assess the soil quality. Loose, sandy, or clay-based soils may require more extensive foundation work, such as deeper piers or a reinforced slab.
- Garage Usage: Determine if your garage will be used for heavy-duty purposes, like housing machinery or providing workspace. A more robust foundation may be necessary for these needs.
- Climate: In colder climates, you may need to account for frost heave, which can cause foundations to shift. Opt for deeper foundations if you live in an area prone to freezing temperatures.
- Budget: Some foundation types, such as a full basement, can significantly increase construction costs. Choose a foundation that balances durability with your available budget.
Choosing the right foundation is not just about stability–it also impacts the overall construction cost and the long-term maintenance of your garage. Make sure to consult with a foundation specialist or contractor to ensure the best fit for your project.
Foundation Comparison Table
Foundation Type | Cost | Durability | Best For |
---|---|---|---|
Slab Foundation | Low | High | Small garages, stable soil |
Pier and Beam | Moderate | Moderate | Uneven soil, heavy-duty use |
Full Basement | High | Very High | Large garages, additional storage |
Crawl Space | Moderate | Moderate | Cost-effective, mild climates |
Selecting Materials for Walls, Roof, and Flooring
When constructing a garage, choosing the right materials for the walls, roof, and flooring is crucial for durability, cost-efficiency, and aesthetic appeal. Each component serves a unique purpose, whether it’s providing structural integrity, ensuring weather resistance, or offering long-term maintenance benefits. The choice of materials depends on the specific needs of your garage and local climate conditions.
Before finalizing your material choices, it is essential to consider factors like insulation, waterproofing, and overall design. This will not only impact the longevity of the garage but also contribute to energy efficiency. Below is a breakdown of suitable materials for each part of your garage construction.
Walls
The walls of your garage can be built using various materials, each offering different benefits.
- Wooden Frames with Siding: Offers a traditional look and is relatively easy to construct. It provides good insulation when combined with the right siding materials.
- Concrete: Known for its strength and durability, concrete walls can withstand harsh weather conditions and provide excellent security.
- Metal: Steel or aluminum panels are a low-maintenance option, offering fire resistance and durability. However, they may require additional insulation to prevent heat loss in colder climates.
Roofing Materials
The roof of the garage must be able to handle the elements while offering longevity and minimal maintenance.
- Asphalt Shingles: A cost-effective and versatile option, asphalt shingles are easy to install and provide good protection from rain and wind.
- Metal Roofing: Durable and long-lasting, metal roofs are resistant to extreme weather conditions and can reflect heat, making them ideal for warmer climates.
- Clay or Concrete Tiles: Known for their aesthetic appeal, these tiles are highly durable and provide excellent thermal insulation, though they come at a higher cost.
Flooring Options
The flooring of your garage should be designed to handle heavy loads, resist moisture, and be easy to maintain. Several options are available depending on the garage's purpose.
Material | Advantages | Disadvantages |
---|---|---|
Concrete Slab | Durable, low-maintenance, and ideal for heavy-duty use. | Can crack over time if not properly sealed or if exposed to extreme weather. |
Epoxy Coating | Provides a smooth, glossy finish that is easy to clean and resistant to stains. | Requires a solid base and can be slippery when wet. |
Interlocking Tiles | Easy to install and replace, ideal for garages used as workshops. | Less durable than concrete or epoxy, and can be prone to shifting or damage under heavy loads. |
Choose materials that best align with your local climate, garage usage, and personal preferences to ensure a durable and functional structure.
Planning for Electrical and Lighting Setup
When designing a new garage, one of the most crucial steps is determining the electrical system and lighting installation. A well-planned electrical setup ensures that the garage functions efficiently and safely, especially when using power tools or other heavy-duty equipment. This involves careful consideration of the number of outlets, wiring types, and the best placement for lights to provide sufficient illumination for all tasks.
Incorporating proper lighting not only enhances visibility but also improves safety. It’s essential to decide where lights will be mounted, what kind of bulbs to use, and whether additional lighting will be required for specific areas, such as workbenches or storage shelves. Furthermore, wiring must be done according to local codes to prevent electrical hazards.
Key Points to Consider
- Assess the overall power requirements of your garage (appliances, lighting, tools, etc.)
- Plan for a sufficient number of outlets at convenient locations
- Ensure proper grounding and circuit protection
Electrical Planning Steps
- Determine the total power needs of the garage, considering the devices and appliances that will be used.
- Install outlets strategically, especially near workstations and high-power equipment.
- Choose the right type of wiring for your garage–usually 12-gauge for most standard tools and appliances.
- Plan for dedicated circuits for large equipment such as air compressors or welders.
Lighting Installation Guide
Light Type | Best Use | Power Consumption |
---|---|---|
LED | General lighting, high brightness | Low |
Fluorescent | Workstations, task lighting | Moderate |
Incandescent | Accent lighting, less common for garages | High |
Important: Always ensure that your electrical system is inspected by a certified electrician to comply with safety regulations and local codes.
Choosing the Right Contractor or Builder for Your Garage
When planning to build a garage, one of the most critical decisions is selecting a professional contractor or builder. A skilled expert will ensure the project runs smoothly, from design to completion, meeting all local regulations and codes. Hiring the right person or team can save you time, money, and unnecessary stress.
To find the best contractor, do thorough research and consider factors like experience, reputation, and availability. A qualified builder will provide clear timelines, offer practical solutions, and communicate effectively throughout the process.
Key Points to Consider When Hiring a Contractor
- Experience and Expertise: Look for a contractor with proven experience in building garages. Specialized knowledge ensures high-quality work and adherence to standards.
- References and Reviews: Check past client testimonials or online reviews to gauge the contractor's reliability and work quality.
- Licensing and Insurance: Ensure the contractor is properly licensed and insured. This protects you from potential liabilities during the project.
- Clear Communication: A good contractor will keep you informed and address any concerns promptly.
Steps to Vet and Hire a Contractor
- Gather Multiple Quotes: Get at least three quotes to compare pricing and scope of work.
- Check Credentials: Confirm licensing, insurance, and bonding to verify their professionalism.
- Review Contract Details: Ensure the contract includes payment schedules, project timelines, and warranties.
"Hiring a qualified contractor isn't just about cost–it's about securing a high-quality, long-lasting garage that adds value to your property."
Contractor Interview Questions
Question | Reason |
---|---|
How many garages have you built in the past year? | Assesses relevant experience. |
Can you provide references from previous clients? | Helps gauge reliability and quality of work. |
What is your estimated project timeline? | Ensures realistic expectations on completion dates. |
Manage the Construction Timeline and Budget
Proper planning is essential to keep the project on track. Managing the construction timeline and budget efficiently requires attention to detail and proactive oversight. Ensure that key milestones are set in advance to avoid unnecessary delays and cost overruns. Tracking the progress against the scheduled completion dates will help prevent last-minute surprises.
Budgeting for the garage construction involves estimating all expenses accurately. This includes labor, materials, permits, and potential unexpected costs. It’s important to leave a buffer for unplanned expenditures to maintain financial flexibility throughout the project.
Tips for Timeline and Budget Management
- Establish a clear project timeline with specific milestones and deadlines.
- Allocate extra funds for unforeseen circumstances, such as material price fluctuations.
- Communicate regularly with the contractor to ensure adherence to both the timeline and budget.
Important: Small changes to the project scope can cause significant delays and increase costs. Always get approval for any adjustments before proceeding.
Key Factors to Monitor
Factor | Description |
---|---|
Labor Costs | Monitor the hours worked and rates to ensure labor doesn’t exceed the estimated budget. |
Materials | Prices can fluctuate, so confirm that materials are ordered and delivered on time to prevent delays. |
Permits | Permit fees and approval times can affect both the budget and timeline. Secure them early to avoid disruptions. |
Final Inspection and Approval from Local Authorities
Once the garage construction is completed, it is crucial to undergo a final inspection by local authorities to ensure compliance with safety regulations, building codes, and zoning laws. This process guarantees that the structure is safe for use and has been built according to the approved plans. The inspection involves a thorough review of various aspects of the project, including the foundation, electrical systems, and overall structural integrity.
After the inspection, the authorities will either approve or deny the garage based on their findings. If the garage passes, a certificate of occupancy will be issued. If any issues are found, the owner will be required to make necessary corrections before the structure can be deemed compliant. Below are the typical steps involved in this process:
Steps for Final Inspection
- Schedule the inspection with local building authorities.
- Ensure all construction is completed according to approved plans.
- Prepare necessary documentation, such as permits and blueprints.
- Pass the inspection or make required adjustments if any issues arise.
- Obtain a certificate of occupancy from the local authorities.
Important Factors to Consider
Note: Ensure all permits and documentation are up to date and available for review during the final inspection. Missing paperwork can delay the approval process.
Common Issues Found During Inspections
Issue | Resolution |
---|---|
Non-compliant electrical wiring | Rewire the system according to local codes. |
Improper foundation depth | Excavate and adjust the foundation to meet regulations. |
Missing fire safety measures | Install required fire extinguishers, alarms, or sprinklers. |