2 Car Garage Barn Plans
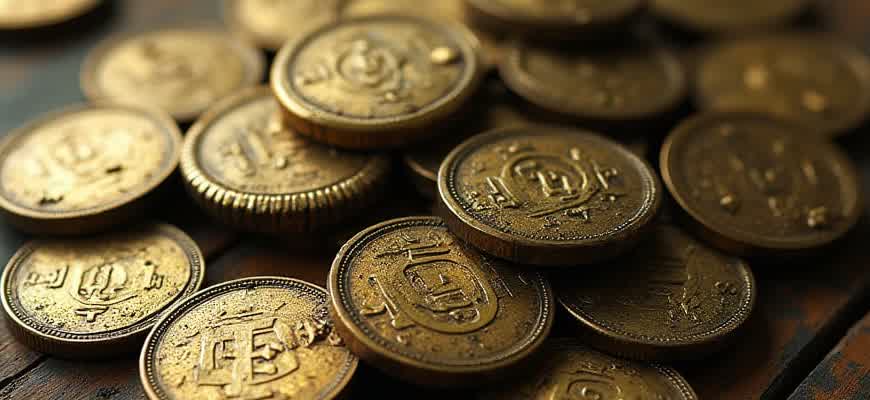
Building a two-car garage barn is an excellent way to combine functionality with aesthetic appeal. These structures offer ample space for both parking and storage, making them a popular choice for homeowners looking to maximize their property. Below are some important considerations when planning your two-car garage barn.
Key Features to Consider:
- Size and layout: Ensure the structure can comfortably fit two vehicles and provide additional space for storage or workshops.
- Materials: Choose durable materials that can withstand weather conditions, such as wood, metal, or a combination of both.
- Roof style: Gable, gambrel, and lean-to roofs are common for garage barns, each offering different aesthetic and practical benefits.
- Entryways: Determine whether you'll need additional side doors, windows, or larger openings for easy access to storage areas.
Design Options:
- Traditional barn-style: Features a steep roof pitch and large doors, ideal for larger vehicles and equipment.
- Modern barn: Offers sleek lines and more compact dimensions while maintaining the rustic charm of a barn structure.
- Workshop-integrated: Includes additional space for tools, workbenches, and storage, catering to DIY enthusiasts.
Before finalizing your design, consider local zoning laws and building codes to ensure compliance and avoid unexpected issues during construction.
Example Design Overview:
Design Type | Size | Features |
---|---|---|
Traditional Barn | 24'x30' | High roof, large doors, storage loft |
Modern Barn | 20'x25' | Simplified roof, clean lines, minimal storage |
Workshop Barn | 30'x40' | Integrated workspaces, extra storage, double doors |
How to Choose the Right Location for Your 2 Car Garage Barn
When planning to build a 2-car garage barn, selecting the ideal location is crucial to ensuring functionality, accessibility, and long-term durability. It is not just about finding a space on your property but also about considering the logistics, traffic flow, and land characteristics. A well-chosen location can enhance your building’s usability and make maintenance easier over the years.
The area you select will directly impact the overall cost and convenience of constructing your garage barn. It is essential to consider factors such as slope, proximity to the road, accessibility, and the surrounding environment. Below are key points to keep in mind during your selection process.
Factors to Consider When Selecting a Location
- Topography: Choose a flat or gently sloped area for easy construction. Avoid building in low-lying areas where water can pool.
- Access: Ensure the location provides easy access for vehicles, with enough room for maneuvering and turning.
- Distance to Utilities: Consider the proximity to water, electricity, and sewage lines if these services are required for your garage barn.
- Privacy and Noise: Select a location that minimizes exposure to loud traffic or other disturbances. A more secluded area may be preferable.
- Zoning and Regulations: Check local zoning laws and building codes to make sure the location is suitable for your project.
Step-by-Step Guide to Finding the Best Spot
- Survey the Property: Walk the entire property to identify areas that meet your topography and access requirements.
- Measure the Space: Make sure the area is large enough to accommodate your garage barn and provide room for future expansion or landscaping.
- Evaluate Sun and Wind Exposure: Consider how the location will be affected by sunlight and wind. Proper orientation can improve energy efficiency and comfort.
- Consult Local Authorities: Verify that the site complies with zoning regulations, setback requirements, and other legal conditions.
Important Tip: Before breaking ground, always consult a professional to ensure that your chosen location will meet all construction and environmental requirements.
Example of Space Requirements for a 2-Car Garage Barn
Dimension | Recommended Measurement |
---|---|
Width | At least 24 feet |
Depth | At least 30 feet |
Driveway | Minimum 15 feet wide |
Understanding the Materials Needed for Building a 2 Car Garage Barn
Building a two-car garage barn requires careful planning and a clear understanding of the materials involved. The choice of materials will impact the structure’s durability, appearance, and cost. The right materials ensure the garage barn can withstand various weather conditions and provide the needed space and functionality for vehicle storage or additional purposes. It is crucial to understand the requirements for both the foundation and the walls, as well as for roofing and finishing details.
When selecting materials, consider factors such as climate, long-term maintenance, and budget. Materials like pressure-treated wood, steel, and concrete are commonly used due to their strength and resilience. Below is an overview of the essential materials that will be required to build a two-car garage barn, broken down by category.
Essential Materials Breakdown
- Foundation Materials:
- Concrete (for slab foundation or footings)
- Rebar (for reinforcement)
- Framing Materials:
- Pressure-treated lumber (for beams and posts)
- Wooden studs (for walls)
- Metal connectors (for framing stability)
- Roofing Materials:
- Asphalt shingles or metal roofing
- Roof trusses or rafters
- Roofing underlayment
- Exterior Finish:
- Siding (wood, metal, or vinyl)
- Paint or stain (for weather protection)
Additional Considerations
Besides the basic materials, there are other components that contribute to the overall function and efficiency of the garage barn:
- Doors and Windows: Garage doors (manual or automated), side doors, and small windows for ventilation and natural light.
- Electrical Systems: Wiring, light fixtures, and outlets for convenience and lighting.
- Insulation: Insulation materials for energy efficiency, particularly in colder climates.
"Choosing the right combination of materials is key to ensuring the garage barn is both functional and durable. The proper use of insulation and weather-resistant finishes can drastically extend the life of the structure."
Material Cost Table
Material | Estimated Cost (per unit) |
---|---|
Concrete (per cubic yard) | $150 - $200 |
Pressure-treated lumber (per board foot) | $2.50 - $4.00 |
Metal roofing (per square foot) | $3.50 - $5.00 |
Asphalt shingles (per bundle) | $30 - $50 |
Siding (per square foot) | $1.50 - $3.00 |
Step-by-Step Instructions for Laying the Foundation of Your Garage Barn
Before beginning the construction of your 2-car garage barn, ensuring a solid and level foundation is crucial for the longevity and stability of the structure. The foundation serves as the base that supports the entire weight of the building, including its walls, roof, and any stored equipment. In this section, we will walk you through the essential steps for preparing and laying a durable foundation.
There are various foundation options depending on the size and soil type, but the most common choices for a garage barn are concrete slab foundations and pier foundations. Each method requires precise planning, so follow the steps carefully to avoid mistakes that could compromise the structural integrity of your barn.
1. Preparing the Site
- Clear the land of any debris, trees, and rocks to create a clean workspace.
- Use a surveyor’s level to measure the land and ensure it is level.
- Mark the perimeter of the foundation using stakes and string.
- Double-check all measurements for accuracy to ensure the foundation aligns with the building plan.
2. Excavating the Foundation Area
Once the site is prepared, excavation is necessary to make room for the foundation. The depth and width of the excavation depend on the type of foundation and local building codes.
- For a slab foundation, excavate to a depth of about 6-8 inches for the slab thickness and an additional few inches for gravel.
- If installing a pier foundation, dig holes at the corners and along the perimeter where the piers will be placed.
- Ensure that the ground is compacted to avoid future settling.
3. Laying the Foundation
Now that the site is prepared and excavated, it’s time to lay the foundation.
Tip: Always check the local building codes before proceeding to ensure compliance with regulations.
- For a concrete slab foundation, spread a layer of gravel at the bottom for drainage.
- Install wooden forms to shape the concrete slab and pour it evenly into the prepared area.
- If using piers, place concrete piers at each marked location and allow them to cure for several days before proceeding.
4. Curing and Final Inspection
Once the foundation is poured, it’s essential to let the concrete cure for at least 7-10 days. During this time, make sure to keep the surface moist to prevent cracking.
Foundation Type | Curing Time |
---|---|
Concrete Slab | 7-10 days |
Piers | 7-10 days |
Design Considerations for Maximizing Space in a 2 Car Garage Barn
When designing a two-car garage barn, optimizing available space is key to ensuring it serves multiple purposes efficiently. Thoughtful planning can transform a standard garage into a versatile storage and workspace area, which is especially important when dealing with limited land. Strategic use of vertical space, organizational features, and flexible layouts are all integral to creating a functional and spacious environment.
To achieve the maximum use of space, it's essential to consider various factors, such as layout, storage options, and accessibility. Each element should be designed to enhance both the usability and comfort of the space. Here are several key strategies that can help in maximizing space within a two-car garage barn design:
Key Strategies for Maximizing Garage Space
- Vertical Storage: Utilize wall-mounted shelves, racks, and cabinets to keep tools, equipment, and seasonal items off the floor.
- Multi-Function Furniture: Incorporate foldable or movable workbenches that can be stored when not in use.
- Overhead Storage: Install lofts or ceiling-mounted storage systems to store bulky or infrequently used items.
- Efficient Door Systems: Opt for roll-up or sliding doors to maximize opening space and reduce swing room requirements.
Floor Plan Optimization Tips
- Plan for a wide vehicle entry point, but avoid large unused spaces in the center.
- Position shelving and storage units along the walls to ensure easy access to all items.
- Ensure that there is a clear path for movement around the garage to prevent congestion and allow for better circulation.
“The key to maximizing space lies in planning for flexibility, accessibility, and vertical utilization. Every inch counts when building a multi-use garage barn.”
Space Allocation Table
Area | Recommended Use |
---|---|
Walls | Storage shelves, tool racks, and hanging cabinets |
Ceiling | Overhead storage racks, hanging storage bins |
Floor | Vehicle parking, clear movement space |
Common Mistakes to Avoid When Constructing a Two-Car Garage Barn
When building a two-car garage barn, careful planning is crucial to ensure both functionality and durability. Many individuals make critical errors during the construction process that can lead to expensive repairs or inefficiencies down the line. Avoiding these mistakes will not only save time but also improve the overall quality of the structure.
While designing a garage barn, common pitfalls often arise from overlooking key aspects of the project, from foundation work to the integration of electrical and ventilation systems. Below are the most common mistakes to avoid during the process.
1. Inadequate Foundation and Site Preparation
One of the most important steps when constructing a garage barn is ensuring a solid foundation. Poor site preparation can lead to structural issues, cracking, or sinking. Pay close attention to the soil type and weather conditions when preparing the foundation.
Tip: Always consult a professional to evaluate the soil condition and ensure proper drainage to prevent future issues.
2. Ignoring Proper Ventilation
Ventilation is often overlooked when building a garage barn, yet it is crucial for preventing moisture buildup, which can cause mold, rot, and rust. Proper airflow helps maintain a safe environment for both vehicles and stored items.
- Install vents at strategic locations, such as the roof and walls.
- Ensure that air can flow freely through the garage to reduce humidity.
3. Failing to Plan for Storage
A two-car garage barn should provide enough space not only for vehicles but also for tools, equipment, and other storage needs. Without a well-thought-out storage plan, you may end up with a cluttered and inefficient space.
- Consider adding shelving or overhead storage units.
- Ensure that the layout allows for easy access to tools and equipment.
4. Miscalculating Electrical Needs
Electrical systems must be designed according to the needs of the space. Failing to account for sufficient outlets or proper wiring can limit the functionality of your garage barn.
Type of Equipment | Recommended Number of Outlets |
---|---|
Tools | 3-5 outlets |
Lighting | 2-4 outlets |
Appliances | 1-2 outlets |
How to Properly Insulate Your 2 Car Garage Barn for Year-Round Use
When it comes to making your two-car garage barn usable throughout all seasons, proper insulation is essential. Insulating the structure not only helps to maintain a comfortable temperature but also protects your investments and reduces energy costs. Understanding how to insulate effectively can turn your barn into a functional space year-round.
To begin with, choosing the right materials and installation method is crucial. Insulation should be applied to the walls, roof, and floor to achieve the best results. Below are key steps to consider when insulating your garage barn.
Key Steps to Insulate Your Garage Barn
- Assess the Current Structure: Before beginning, check for any gaps or cracks that may allow air to leak in. Sealing these areas will ensure maximum insulation performance.
- Choose the Right Insulation Material: Common options include fiberglass batts, spray foam, and foam boards. Each has different advantages depending on your climate and budget.
- Insulate the Walls: Apply your chosen insulation to the interior of the walls. Ensure it fits snugly, without gaps, to maintain an airtight seal.
- Install Insulation in the Roof: The roof is one of the most critical areas. Use high-quality insulation here to prevent heat loss in winter and excessive heat gain in summer.
- Consider Insulating the Floor: If your garage barn is directly on the ground, consider adding a layer of insulation to the floor to prevent cold drafts from seeping in.
Common Insulation Materials
Material | Advantages | Disadvantages |
---|---|---|
Fiberglass Batt | Affordable, easy to install | Can be irritating to skin, less effective in extreme climates |
Spray Foam | Seals gaps well, high R-value | More expensive, requires professional installation |
Foam Board | Rigid, great for walls and floors | Can be difficult to fit around irregular spaces |
Proper insulation increases the lifespan of your garage barn, prevents moisture buildup, and provides a more energy-efficient space throughout the year.
Cost Breakdown: What to Expect When Building a 2-Car Garage Barn
Building a two-car garage barn involves a combination of structural, design, and finishing costs. The overall price can vary greatly depending on factors such as materials, location, and the complexity of the design. The key is to account for all potential costs to avoid surprises during construction.
Typical expenses include site preparation, foundation work, the structure itself, roofing, and finishes. In some cases, there may also be additional costs for electrical work, insulation, and special features. Below is an outline of common expenses to consider when planning a two-car garage barn.
Key Costs to Consider
- Site Preparation: Includes clearing land, leveling the ground, and any required excavation work.
- Foundation: A concrete slab is commonly used, though the price can increase if additional work like footings is needed.
- Structure: The cost of framing materials like wood or steel will affect the overall cost. Steel framing can be more expensive but may offer greater durability.
- Roofing: The type of roofing material, such as metal or asphalt shingles, can impact the cost significantly.
- Finish Work: Interior insulation, drywall, and exterior finishes like siding will add to the cost.
Estimated Cost Breakdown
Item | Estimated Cost |
---|---|
Site Preparation | $1,000 - $3,000 |
Foundation | $5,000 - $8,000 |
Structure (Framing) | $10,000 - $15,000 |
Roofing | $3,000 - $5,000 |
Finish Work | $4,000 - $6,000 |
Important Note: These costs are estimates and can vary depending on location, materials, and design choices. Always consult with a local contractor for more accurate pricing tailored to your specific needs.
Additional Costs to Consider
- Electrical Work: Adding electricity for lights, outlets, or HVAC systems can add $2,000 - $5,000.
- Permits and Inspections: Required permits may cost anywhere from $500 to $2,000 depending on local regulations.
- Landscaping: If you plan to add a driveway or landscaping, budget for an additional $2,000 - $4,000.
Legal Considerations and Necessary Approvals for Building a Two-Car Garage Barn
When planning to build a two-car garage barn, it is crucial to understand the legal requirements and obtain the necessary permits. Regulations vary depending on the location, and failing to comply with them can result in fines or the need to dismantle the structure. The key steps to ensure compliance with local laws include understanding zoning regulations, building codes, and environmental impact considerations.
The first step is to determine if the construction falls under any specific zoning regulations for residential or agricultural properties. Local authorities typically define the dimensions, height restrictions, and proximity to property boundaries for such structures. Additionally, construction in certain flood zones or areas with historical significance may require extra permits or approvals.
Key Legal Requirements to Consider
- Zoning Laws: Verify the zoning classification of your property to ensure a garage barn is allowed and check any restrictions that may apply, such as size or location.
- Building Permits: Almost every construction project requires a building permit. Contact local authorities to confirm the required permits and application process.
- Site Plans and Drawings: Most jurisdictions require detailed plans of the proposed structure, including measurements, construction materials, and site layout.
- Environmental Concerns: Some areas may have additional environmental restrictions, such as managing stormwater runoff or protecting local wildlife habitats.
Steps to Obtain Permits
- Consult Local Authorities: Begin by reaching out to the local planning department to understand the permit requirements and timelines.
- Submit Application and Plans: Complete the permit application, ensuring all required documents such as site plans, architectural drawings, and engineering reports are included.
- Schedule Inspections: After approval, your project may require inspections during various stages of construction to ensure compliance with building codes.
- Receive Final Approval: Once construction is completed, a final inspection is typically required to verify that the structure adheres to all regulations.
Important Information to Keep in Mind
Always check with your local building department about the latest requirements, as regulations may change and differ significantly between regions.
Permit Type | Required Documentation |
---|---|
Building Permit | Site plans, construction details, engineering reports |
Environmental Permit | Impact assessment, stormwater management plan |