3 Bay Garage Cost
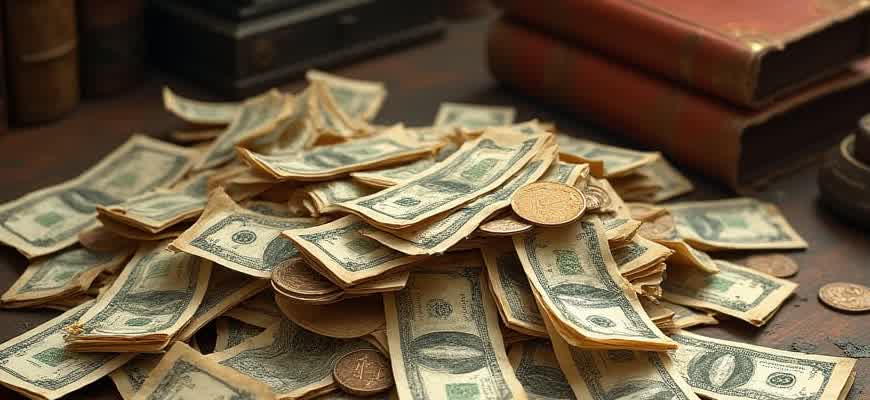
When considering the construction of a 3-bay garage, various factors come into play that affect the overall price. The size, materials used, and geographical location are key determinants in the final cost. Below is a breakdown of some essential elements to consider before starting a project:
- Size and Design Complexity
- Materials: Wood, Steel, or Concrete
- Labor Costs by Region
- Additional Features: Insulation, Electricity, Storage
On average, the cost to build a standard 3-bay garage typically ranges between $30,000 and $60,000. This estimate includes basic construction, but several optional features can drive the price up:
- Basic Structure: $30,000 - $40,000
- Upgraded Materials: $40,000 - $50,000
- Custom Features: $50,000 - $60,000+
"Additional costs can arise from site preparation, permit fees, and labor expenses, depending on your location."
Factors Influencing the Cost of a Three-Bay Garage
When planning to build a three-bay garage, several factors can significantly affect the overall cost. Understanding these elements is essential for budgeting and making informed decisions throughout the construction process. Costs can fluctuate based on location, materials, size, and additional features, all of which play a crucial role in determining the final price of the project.
Below are the key considerations that can impact the price of a three-bay garage:
Key Factors Affecting Garage Costs
- Location: Regional differences in labor and material prices can lead to significant variations in cost.
- Materials: The type of materials used, such as wood, steel, or brick, directly influences both the durability and cost of the garage.
- Size: A larger garage requires more materials and labor, thereby increasing the price.
- Design and Features: Custom features like windows, insulation, electrical work, or a loft area add to the overall expense.
- Foundation: The complexity of the foundation required (e.g., slab or raised) can impact the cost significantly.
Additional Cost-Influencing Aspects
Additional elements such as the type of roof, garage doors, and the inclusion of a work area or storage space can also increase the overall project cost.
- Roofing: The choice between a simple gable or more complex roof styles affects material costs.
- Garage Doors: Custom or high-end doors will contribute to the price, especially if automation or insulation is involved.
- Storage and Work Areas: Adding extra storage space or workbenches increases both material and labor costs.
Cost Breakdown by Key Elements
Element | Average Cost |
---|---|
Basic Materials | $10,000 - $15,000 |
Labor | $5,000 - $10,000 |
Garage Doors | $2,000 - $5,000 |
Additional Features | $3,000 - $8,000 |
Comparing Material Costs for 3 Bay Garage Construction
When building a three-bay garage, the choice of materials plays a crucial role in determining the overall cost of the project. Each material offers distinct benefits in terms of durability, aesthetics, and price. Understanding the cost differences between these materials will help homeowners make informed decisions when planning their garage construction.
The primary materials commonly used for garage construction include wood, steel, and concrete. Each material has its own set of advantages and disadvantages, which directly impacts the final price of the project. Below is a comparison of the material costs typically encountered during the construction of a three-bay garage.
Material Cost Comparison
Material | Cost per Square Foot | Pros | Cons |
---|---|---|---|
Wood | $25 - $40 | Affordable, traditional look, easy to modify | Less durable, requires regular maintenance |
Steel | $35 - $55 | Strong, low maintenance, fire-resistant | Higher initial cost, less customizable |
Concrete | $50 - $75 | Extremely durable, energy efficient | Expensive, difficult to modify |
Each material has its advantages based on the specific needs and preferences of the homeowner. For example, while wood is the most affordable option, it may require more upkeep over time compared to steel or concrete, which offer superior durability and longevity.
It is important to consider long-term maintenance costs when choosing materials. While steel and concrete may have a higher upfront cost, they often require less maintenance over the years compared to wood.
Additional Factors Affecting Costs
- Location of construction
- Foundation requirements
- Design complexity
- Labor costs
These factors can significantly influence the material choice and overall cost of the project. Homeowners should also factor in local building codes and weather conditions when deciding on the best material for their garage construction.
Labor Costs for Constructing a 3-Bay Garage
When building a 3-bay garage, labor expenses play a significant role in the overall cost of the project. These costs can vary greatly depending on the location, the complexity of the construction, and the specific contractors hired. Labor fees typically include wages for a range of specialists, from general contractors to carpenters, electricians, and plumbers, if needed. Understanding the breakdown of these labor costs is essential for budgeting effectively.
The labor required for such a project generally involves several stages, including site preparation, foundation work, framing, roofing, and finishing. Each phase requires skilled professionals to ensure that the construction is completed safely and efficiently. In some cases, you might need additional experts for specialized tasks, such as electrical work or garage door installation. Below is a detailed breakdown of the typical labor costs for each stage of construction:
Typical Labor Cost Breakdown
- Site Preparation: This includes clearing the land, leveling, and excavation. Labor for this phase may cost between $1,000 to $3,000 depending on the site’s condition.
- Foundation Work: Pouring the foundation and ensuring proper curing. This can range from $2,500 to $6,000, depending on the size and complexity.
- Framing and Structure: This phase involves the framing of walls, roof trusses, and other structural components. Costs typically range from $4,000 to $8,000.
- Roofing: Installing the roof with materials like shingles or metal. Roofing labor can cost anywhere from $2,000 to $5,000.
- Finishing Work: Includes drywall, insulation, and any interior or exterior finishing. This can range from $3,000 to $7,000.
Labor costs often account for approximately 30% to 50% of the total cost of constructing a 3-bay garage, depending on the complexity and regional wage differences.
Labor Rates by Region
Region | Average Labor Cost per Hour |
---|---|
Northeast | $50 - $75 |
Midwest | $40 - $60 |
South | $35 - $55 |
West | $45 - $70 |
Labor rates vary widely by region, so it is important to get multiple estimates to ensure you are paying competitive rates for the services in your area.
Additional Features and Their Impact on 3 Bay Garage Prices
When considering the cost of a three-car garage, additional features can significantly influence the final price. These upgrades not only enhance the functionality of the garage but also improve its aesthetic appeal. However, it’s important to weigh the added costs carefully to ensure they align with your budget and needs. Some features offer better long-term value, while others might only add to the initial expense without providing much return on investment.
Common upgrades include enhanced door systems, insulation, flooring choices, and added storage options. Each of these features contributes differently to the overall cost, depending on the materials used and the complexity of installation. Let’s explore some of the most popular enhancements and their potential impact on the total price.
Key Features That Affect Garage Prices
- Insulation: Proper insulation can increase the cost by $500-$2,000 depending on the material and method used. It’s especially valuable in colder climates for temperature control.
- Upgraded Doors: Custom or high-quality garage doors can add $1,000-$5,000. Insulated or automatic doors often come at a premium.
- Flooring: Concrete floors are the most common, but epoxy or polished flooring adds another $1,000-$3,000.
- Storage Options: Built-in shelves or attic storage may cost between $500 and $2,500, depending on the design and materials.
- Windows: Adding windows to the garage for natural light and ventilation can add $500-$2,000.
Potential Cost Breakdown of Added Features
Feature | Cost Range |
---|---|
Insulation | $500 - $2,000 |
Upgraded Doors | $1,000 - $5,000 |
Flooring | $1,000 - $3,000 |
Storage Options | $500 - $2,500 |
Windows | $500 - $2,000 |
Important: While upgrading features can increase your garage's functionality and comfort, it is crucial to consider the long-term costs and maintenance associated with these enhancements.
Cost Differences: Prefabricated vs. Custom 3 Bay Garages
When it comes to building a 3-bay garage, the cost can vary significantly depending on whether you opt for a prefabricated or a custom design. Each approach offers unique benefits and challenges, and understanding these differences can help you make an informed decision based on your budget and needs. Prefabricated garages are typically mass-produced, which can make them more affordable, while custom garages are tailored to your specific requirements, resulting in a higher cost. Below, we'll explore these two options in more detail to help you compare their costs and benefits.
The primary cost difference between prefabricated and custom-built garages lies in the materials, construction time, and level of personalization. Prefabricated garages usually come with a set design and standardized features, leading to lower labor costs and quicker installation. Custom garages, on the other hand, allow for full control over the design, materials, and finishes, but this flexibility often leads to a significant increase in both the price and construction time.
Comparison of Cost Factors
- Materials: Prefabricated garages use pre-made materials, which can be purchased in bulk, lowering costs. Custom garages use higher-quality or specialty materials, driving up the cost.
- Construction Time: Prefabricated garages are quicker to assemble, reducing labor costs. Custom garages take longer to build, leading to higher labor costs.
- Design Flexibility: Custom garages offer complete design freedom, which can increase the overall cost due to the need for architectural plans and custom construction.
Cost Breakdown
Type of Garage | Average Cost | Time to Build |
---|---|---|
Prefabricated | $15,000 - $30,000 | 1 - 2 weeks |
Custom | $35,000 - $75,000 | 2 - 6 months |
Custom-built garages provide a high level of personalization, but the cost and time investment are significantly higher than prefabricated models.
Estimating Costs of Permits and Regulations for a 3-Bay Garage
When building a 3-bay garage, it is crucial to account for various fees and legal requirements. Permits and regulations vary depending on local jurisdiction, and understanding these costs upfront can help avoid delays and unexpected expenses. These fees can include everything from the initial permit application to inspections during and after construction. Compliance with zoning laws, building codes, and environmental standards is essential in ensuring that the construction process proceeds smoothly and legally.
Additionally, there may be additional costs for specific permits related to electrical work, plumbing, or if the garage is intended to include living space or storage. It is important to research the exact requirements for your area to get a clear picture of all associated costs. Below are some typical expenses and considerations you may encounter when applying for permits and following regulations.
Common Permit Costs and Regulations
- Building Permits: Typically required for the overall construction of the garage.
- Electrical Permits: If your garage includes electrical work, an electrical permit may be necessary.
- Plumbing Permits: If the garage has plumbing fixtures, such as a sink or a bathroom, you may need a plumbing permit.
- Zoning Permits: Ensure the garage complies with local zoning laws related to size, placement, and use.
- Environmental Impact Assessments: In some areas, this may be required if the construction could affect the environment.
Regulations to Keep in Mind
- Building Codes: Local regulations may include specific materials, foundation types, or height restrictions.
- Zoning Restrictions: These govern the location and size of the structure on your property.
- Fire Safety Regulations: Ensure compliance with local fire codes for proper fire exits, sprinklers, and other safety measures.
Typical Costs for a 3-Bay Garage Construction
Permit Type | Estimated Cost |
---|---|
Building Permit | $300 - $1,500 |
Electrical Permit | $100 - $500 |
Plumbing Permit | $50 - $300 |
Zoning Permit | $200 - $1,000 |
Environmental Impact Assessment | $500 - $2,000 |
Note: Costs can vary widely based on your location, the complexity of the project, and the size of the garage. Always check with local authorities for the most accurate and up-to-date information.
Budgeting Tips for a Cost-Effective 3 Bay Garage Construction
Building a 3-bay garage can be a significant investment, but with proper planning and budgeting, you can achieve a high-quality structure without overspending. It's essential to consider various factors such as materials, labor, and permits while keeping costs under control. Below are some tips to help you plan your budget effectively.
Start by assessing the total cost of the garage project, which includes not only the construction itself but also any additional costs such as site preparation, utilities, and potential unexpected expenses. By breaking down these components, you'll have a clear view of where to allocate your resources.
Smart Ways to Save on Construction Costs
- Choose affordable materials – Opt for cost-effective yet durable materials like steel or wood frame construction to reduce overall material costs.
- Plan for efficient space usage – Design your garage layout to maximize usable space without excessive square footage, reducing both material and labor costs.
- Get multiple quotes – Always obtain quotes from at least three contractors to ensure you're getting a competitive price for labor and materials.
Common Cost-Saving Areas to Consider
- Foundation – Choose a simple slab or gravel foundation over more complex options like a full basement, which can significantly reduce expenses.
- Permits – Check local zoning laws and building codes. Sometimes, a smaller garage may not require as many permits, saving time and money.
- DIY Projects – If you're handy, consider taking on some parts of the construction yourself, like painting or installing insulation.
Cost Breakdown Table
Component | Estimated Cost |
---|---|
Foundation | $5,000 - $10,000 |
Materials | $12,000 - $18,000 |
Labor | $8,000 - $12,000 |
Permits & Fees | $1,000 - $3,000 |
Utilities & Site Prep | $2,000 - $5,000 |
Tip: Always set aside a contingency fund of 10-15% of your total budget to cover unexpected costs during the project.