Industrial Garage Conversion
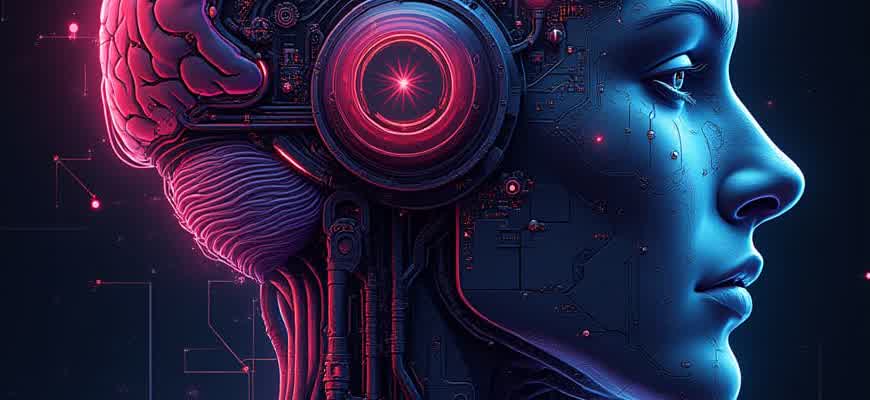
Converting an industrial garage into a usable space involves more than just a few cosmetic changes. The process requires careful planning to ensure the building meets new functional requirements while maintaining safety standards. Below are key steps and considerations for a successful transformation:
- Evaluate the existing structure: Assess the condition of walls, foundation, and roof.
- Determine the intended purpose: Will it be an office, apartment, or studio?
- Address utilities: Plumbing, electricity, and HVAC systems may need upgrades.
Key considerations before starting:
"The structural integrity of the building should be a top priority, especially when converting industrial spaces. Any renovations must adhere to local building codes and safety regulations."
Here's a breakdown of common steps involved in the garage conversion process:
Step | Details |
---|---|
1. Structural Assessment | Ensure the garage is sound enough for modifications. |
2. Zoning Approval | Verify if the local zoning laws allow for residential or commercial use. |
3. Utilities Setup | Install or upgrade plumbing, electrical, and HVAC systems as needed. |
Evaluating Garage Conversion Suitability
Before diving into a garage conversion project, it's crucial to assess whether the structure of your garage is suitable for the transformation you have in mind. Certain factors, such as size, structural integrity, and legal considerations, will determine if your garage can be effectively converted into a functional living or working space. Proper evaluation helps ensure that you won't face unexpected costs or legal hurdles down the road.
This process begins with a detailed inspection of the garage's current state. You should take into account the foundational strength, roof condition, wall stability, and insulation quality. Additionally, accessibility to utilities like electricity, plumbing, and heating must be considered, as retrofitting these systems can add complexity and cost to your conversion project.
Key Considerations for Garage Conversion
- Size and Layout: Evaluate the available space for your intended use. A larger garage offers more flexibility, while a smaller one might limit your options.
- Structural Integrity: Inspect the foundation, walls, and roof. Any signs of damage or weakness could require extensive repairs before proceeding.
- Legal Permissions: Verify zoning regulations and obtain necessary permits. Local laws may restrict certain types of conversions or require additional work to meet building codes.
- Utilities Access: Consider if the space can be easily connected to essential utilities like water, electricity, and HVAC systems.
Step-by-Step Evaluation Process
- Start by measuring the total square footage of your garage and ensure that it aligns with your conversion needs.
- Inspect the foundation for cracks, settling, or signs of water damage that could impact the integrity of the conversion.
- Check the roof for leaks, missing shingles, or other damage that might require repairs before converting the space.
- Review the walls and doors, ensuring they are sturdy and can support insulation or structural modifications.
- Assess utility access and the feasibility of extending plumbing or electrical lines into the garage if needed.
"It’s essential to address potential structural issues early on to avoid costly repairs after starting the conversion process."
Cost and Time Considerations
Factor | Estimated Cost |
---|---|
Foundation Repair | $2,000 - $5,000 |
Roof Repairs | $1,500 - $4,000 |
Utility Installation | $1,000 - $7,000 |
Permits and Legal Fees | $500 - $3,000 |
Key Permits and Regulations for Industrial Garage Renovations
When transforming an industrial garage into a functional living or commercial space, understanding the required permits and regulations is crucial for ensuring a smooth renovation process. These permits are designed to ensure safety, sustainability, and compliance with local zoning laws. Renovation projects may require permits for electrical, plumbing, structural changes, and environmental factors. Failure to acquire the necessary permits can result in costly fines and delays, so it’s important to understand what is needed before starting.
In addition to permits, there are various regulations that must be followed to ensure that the conversion is both legal and safe. These can vary greatly depending on the location of the industrial garage, the intended use of the space, and the scale of the project. Below are the key permits and regulations to consider when planning an industrial garage renovation.
Common Permits for Industrial Garage Conversions
- Building Permit: Required for any structural modifications, including changes to walls, roofing, or foundations.
- Electrical Permit: Necessary for any new wiring, installation of outlets, or electrical panel upgrades.
- Plumbing Permit: Required for new plumbing lines, fixtures, or drainage systems.
- HVAC Permit: Needed for the installation or modification of heating, ventilation, and air conditioning systems.
Regulations to Consider
- Zoning Laws: Ensure the property is zoned for residential or commercial use depending on your intended purpose.
- Building Codes: Compliance with local building codes, including accessibility, safety, and structural integrity standards.
- Environmental Codes: Consider any environmental impact such as waste management and energy efficiency requirements.
Important Information to Keep in Mind
"Before starting any renovation, always check with local authorities for the specific permits required in your area. Rules can vary greatly depending on your location and the scope of your project."
Permit Application Process
Step | Details |
---|---|
1. Initial Consultation | Meet with local building department to understand required permits. |
2. Submit Plans | Provide detailed blueprints of the intended renovation to obtain approval. |
3. Review and Approval | Wait for permit review and approval before proceeding with the project. |
Choosing the Right Materials for Your Industrial Garage Transformation
When converting a garage into a functional living space, selecting the right materials is crucial to ensure both durability and aesthetics. An industrial-style transformation requires materials that offer a raw, authentic feel while maintaining practicality. The key is to strike a balance between visual appeal, functionality, and long-term resilience. Whether you're designing a home office, studio, or living area, the materials you choose will heavily influence the overall vibe and usability of the space.
It's important to consider how materials interact with the environment and contribute to energy efficiency, soundproofing, and structural integrity. Here are some factors to keep in mind when selecting the materials for your project.
Essential Materials for Industrial Garage Conversions
- Concrete Floors: Offers a robust and raw aesthetic, ideal for the industrial look. It’s also easy to clean and maintain.
- Exposed Steel Beams: A hallmark of industrial style, these beams add strength and a sleek, modern edge to the design.
- Wooden Accents: Combining wood with metal creates warmth, balancing the otherwise cold industrial elements.
- Glass Panels: Large windows and glass doors allow natural light, helping to open up the space and blend interior and exterior.
Things to Consider
- Climate Control: Choose insulation materials like spray foam or fiberglass to prevent heat loss and manage temperature changes.
- Durability: Opt for materials that can withstand the wear and tear of daily use, especially in high-traffic areas.
- Maintenance: Select finishes and coatings that require minimal upkeep, such as polished concrete or treated steel, to maintain the look without constant care.
"Choosing the right materials goes beyond aesthetics–it's about ensuring the space will serve its function for years while capturing the essence of industrial design."
Material Comparison Table
Material | Pros | Cons |
---|---|---|
Concrete | Durable, easy to clean, authentic industrial look | Cold, may require sealing to prevent staining |
Steel | Strong, modern appearance, low maintenance | Can rust without proper treatment, may need reinforcement |
Wood | Warmth, contrast with metal, versatile | Requires more maintenance, can wear over time |
Incorporating Industrial Design Features in a Converted Garage
Transforming a garage into a functional industrial space involves more than just rearranging furniture. The key is to blend raw, industrial elements with the layout to create a cohesive, visually striking environment. Whether it's for a home office, studio, or living space, integrating the right materials and design choices will bring out the full potential of the space.
Start by embracing the natural materials that define industrial style. Exposed brick, metal fixtures, and wooden accents are fundamental to achieving the desired aesthetic. These elements not only enhance the visual appeal but also improve the overall functionality of the space.
Essential Elements to Include in Your Industrial Garage Conversion
- Exposed Beams and Pipes: Highlighting the structural features like beams and pipes adds authenticity. Opt for painted or raw finishes for a more rustic feel.
- Metal and Steel Furniture: Incorporate metal shelving, steel tables, or reclaimed furniture to maintain an industrial vibe.
- Concrete or Wooden Floors: A polished concrete floor or aged wood gives the space a grounded, rugged look.
- Large Windows or Factory-Style Glass: Enhance natural light by installing oversized windows or steel-framed glass panes that reflect industrial architecture.
Key Design Strategies
- Keep It Open: Embrace open shelving and minimalist layouts to highlight the space’s industrial characteristics.
- Color Palette: Use neutral tones like gray, black, and earthy browns, but add contrast with bold metal accents or pops of color in accessories.
- Lighting: Industrial-style lighting, such as exposed filament bulbs or vintage pendant lamps, provides both function and style.
“Industrial design is about revealing the raw beauty of a building's framework. The goal is not just decoration, but a way of life that values simplicity, durability, and authenticity.”
Example Layout Table
Area | Suggested Industrial Elements |
---|---|
Walls | Exposed brick, concrete, or metal paneling |
Floor | Polished concrete or reclaimed wood |
Furniture | Reclaimed wood, steel-framed pieces |
Lighting | Exposed bulbs, factory-style sconces |
Step-by-Step Guide to Electrical and Plumbing Installation in Converted Garages
Converting a garage into a functional living or working space requires careful planning, especially when it comes to electrical and plumbing systems. These installations are essential to ensure the new space meets modern safety standards while also providing necessary utilities. Proper execution can prevent costly repairs in the future and ensure long-term functionality of your converted space.
Electrical and plumbing installations in a converted garage follow similar processes to those in new builds, but they require attention to the specific layout and unique characteristics of the garage structure. Below is a detailed guide to help you understand the essential steps involved in both of these systems.
Electrical System Installation
- Planning the Electrical Layout: Before starting, map out the placement of outlets, lighting, and appliances. Consider the power load and the best way to route wires.
- Obtaining Permits: Always check with local authorities to obtain the necessary permits for electrical work. Failing to do so may result in fines or safety issues.
- Wiring and Circuit Installation: Install the appropriate gauge wiring for outlets and lighting. Ensure that circuits are properly labeled to avoid overloads.
- Install Breaker Panel: If your garage conversion requires additional circuits, you may need to upgrade your breaker panel to handle the load.
- Test the System: After installation, conduct a thorough inspection to ensure the system is functioning correctly and safely.
Plumbing System Installation
- Planning Plumbing Fixtures: Determine where plumbing fixtures such as sinks, toilets, and showers will be installed. This helps with positioning pipes and drains.
- Water Supply and Drain Lines: Run water supply lines from the main source, ensuring proper sizing for the fixtures. Drain lines must be sloped to allow for proper drainage.
- Ventilation for Waste Lines: Proper ventilation is crucial for the plumbing system. Install vent pipes to prevent siphoning and allow wastewater to flow freely.
- Testing for Leaks: Once plumbing is installed, conduct a pressure test to ensure no leaks are present in the system.
Important: Always use licensed professionals for both electrical and plumbing work, especially if you're unfamiliar with the systems. This will ensure safety and compliance with building codes.
Summary Table: Key Steps in Electrical and Plumbing Installation
Task | Electrical Installation | Plumbing Installation |
---|---|---|
Planning | Map out outlets, lighting, and circuits | Determine fixture placement and layout |
Permits | Obtain required electrical permits | Ensure plumbing permits are in place |
Installation | Run wiring and install circuits | Install water and drain lines |
Testing | Check for correct operation and safety | Test for leaks and pressure issues |
Maintenance Tips for Long-Term Durability of Your Converted Garage
Transforming your industrial garage into a functional living or work space requires not only thoughtful design but also regular upkeep to ensure its longevity. Whether you're using the space for storage, as a workshop, or even as a living area, maintaining the structural integrity and aesthetics of the converted garage is essential for maximizing its usability over time.
Here are some practical tips to ensure the durability and smooth operation of your converted garage, with special attention to key elements such as flooring, insulation, and HVAC systems.
Essential Maintenance Practices
- Inspect the Roof Regularly: Ensure that the roof is free from leaks and debris. A simple inspection twice a year can prevent costly water damage and structural weakening.
- Maintain Proper Insulation: Check insulation materials in the walls, ceilings, and floors. Over time, insulation can degrade, causing heat loss and reducing energy efficiency.
- Examine Flooring for Cracks: Concrete floors are common in garage conversions. Regularly inspect for cracks or signs of wear, and seal any gaps promptly to avoid water penetration.
- HVAC System Check-Up: Perform regular maintenance on HVAC systems to ensure consistent airflow and heating/cooling efficiency. Replace filters every 3-6 months.
Routine Checks and Improvements
- Test Electrical Components: Inspect wiring, outlets, and switches for signs of damage or malfunction to prevent potential safety hazards.
- Re-seal Windows and Doors: Check for air leaks or drafts around windows and doors, which can lead to higher energy bills and temperature imbalances.
- Monitor Humidity Levels: Excess moisture can damage both the structure and any furniture or equipment. Use a dehumidifier if necessary to maintain a stable environment.
Important: Always consult with a professional if you notice significant damage or issues that are beyond your skill level. Proactive maintenance can save you from costly repairs in the long run.
Maintenance Checklist
Task | Frequency | Details |
---|---|---|
Roof Inspection | Twice a Year | Look for leaks, debris, and cracks. |
HVAC System Service | Annually | Check airflow and change filters. |
Floor Crack Sealing | As Needed | Check for cracks and seal immediately to prevent water damage. |
Electrical System Check | Annually | Inspect wiring, outlets, and switches for safety. |