Building a Garage for My Business
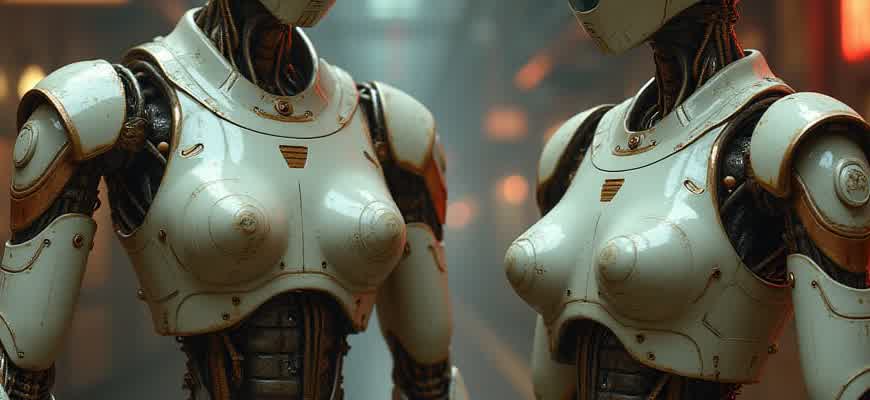
Creating a dedicated workspace for my business requires careful planning and execution. The objective is to build a garage that accommodates both storage and operations, supporting the needs of my growing enterprise. Here are the key considerations for this project:
- Optimal location with easy access to transportation
- Space management to support equipment and staff
- Security and safety measures for valuable assets
Before breaking ground, I need to review a few essential factors to ensure the space is functional:
- Site Analysis – Assessing land quality, zoning, and regulations
- Design Plans – Drafting blueprints that integrate workflow efficiency
- Permits – Ensuring all legal requirements are met before construction begins
Tip: Consider future scalability; the garage should allow for expansion as your business grows.
The project will follow a step-by-step approach to ensure smooth progress, focusing on both quality construction and cost-efficiency.
Phase | Timeline | Key Actions |
---|---|---|
Pre-Construction | 2 weeks | Site preparation, permits, and foundation work |
Building | 6 weeks | Structure assembly, roofing, and installation of utilities |
Post-Construction | 1 week | Final inspection, security checks, and equipment setup |
Choosing the Ideal Spot for Your Business Garage
Picking the right location for your business garage is a crucial step in ensuring smooth operations. The area you choose will impact both day-to-day logistics and long-term profitability. Factors such as accessibility, proximity to suppliers, and zoning regulations play a significant role in the decision-making process. Evaluating all aspects of your potential site will help optimize the functionality of your garage and reduce operational costs.
Before settling on a final location, consider how it aligns with your business needs. Will it provide easy access for customers and deliveries? Is it situated in an area that allows for future expansion? These are just some of the critical considerations to keep in mind when narrowing down your options.
Key Considerations for Location Selection
- Accessibility: Ensure that your garage is easily reachable by both your team and customers. Proximity to major roads or highways can save time and reduce transportation costs.
- Proximity to Suppliers and Clients: Choose a location that minimizes travel time for raw materials and deliveries, as well as for any client visits.
- Zoning Requirements: Verify that the area is zoned for commercial use, specifically for a garage. Failing to comply with local regulations could lead to costly delays.
Steps to Evaluate Potential Locations
- Research Local Zoning Laws: Confirm that the location complies with city or county zoning ordinances for a garage business.
- Check Accessibility: Analyze traffic flow, road conditions, and parking availability for both clients and employees.
- Assess Future Growth Potential: Consider whether the location can accommodate potential expansion or changes in demand.
"Choosing a location is not just about what works now, but about what will continue to work as your business grows and evolves."
Comparison of Different Locations
Location | Accessibility | Cost | Future Expansion |
---|---|---|---|
Downtown Area | High | High | Limited |
Suburban Industrial Park | Moderate | Medium | High |
Rural Location | Low | Low | Moderate |
Calculating the Space Requirements for Your Garage
When planning a garage for your business, accurately estimating the space you need is essential for efficient operations. The amount of room you allocate will determine how comfortably equipment, vehicles, and staff can operate. Insufficient space can lead to congestion, slowdowns, and ultimately, lost productivity. A well-thought-out space plan will ensure that your garage meets the specific demands of your business, while also offering room for future growth.
To calculate your garage's space requirements, you'll need to consider several factors, including the type of vehicles or equipment you plan to store, the number of people working in the space, and any additional areas like storage or maintenance zones. Start by defining the core functions of the garage and assessing the space needed for each function individually.
Key Factors to Consider
- Vehicle Size: Estimate the size of each vehicle, including any oversized equipment or machinery, and factor in space for movement around them.
- Storage Needs: Consider the amount of space needed for storing tools, spare parts, and other materials.
- Work Zones: Allocate areas for vehicle repairs, maintenance, or assembly, ensuring enough room for movement and workspace safety.
Steps for Space Calculation
- Measure the size of your largest vehicle or equipment.
- Include the space required for movement between vehicles and equipment.
- Factor in the number of workstations or staff areas needed for productivity.
- Consider future expansion or additional equipment.
Note: Always account for extra space to accommodate unexpected changes in operations or the introduction of new equipment.
Sample Space Planning Table
Area | Dimensions (ft) | Purpose |
---|---|---|
Vehicle Storage | 12 x 24 | Room for one vehicle |
Workstation | 10 x 10 | Area for tools and repairs |
Storage Area | 8 x 10 | Space for parts and supplies |
Understanding Local Zoning Regulations and Required Permits
When constructing a garage for your business, it's essential to familiarize yourself with the local zoning regulations to ensure the project complies with city or county rules. Zoning laws control how land can be used, including restrictions on the size, location, and purpose of buildings. These laws can vary significantly depending on where you are located, and failing to comply can lead to costly delays or even project shutdowns.
Before you begin construction, check if your property is zoned for the intended use. Local government agencies, such as the zoning office or building department, can provide you with a zoning map and a list of specific requirements. Additionally, you will likely need to obtain various permits before starting the construction process.
Key Considerations for Zoning and Permits
- Zoning Classification: Determine if your property is in a commercial or industrial zone and whether garages are permitted in that zone.
- Building Setbacks: Ensure the garage's location meets setback requirements from property lines, streets, and other structures.
- Size and Height Limits: Be aware of any restrictions on the size and height of the garage based on the local zoning laws.
- Parking Requirements: Confirm if there are specific rules regarding the number of parking spaces or driveway access for your garage.
Typical Permits Required
- Building Permit: Required for the construction of the garage to ensure it meets safety and structural standards.
- Electrical Permit: If you're planning to install electrical systems in the garage, an electrical permit will be necessary.
- Plumbing Permit: If plumbing work is involved, such as installing drains or water lines, a plumbing permit is required.
- Certificate of Occupancy: Once the garage is completed, this certificate ensures that it meets all building codes and is safe for use.
Additional Considerations
Permit Type | Required Documentation |
---|---|
Building Permit | Architectural plans, site plan, and engineering reports |
Electrical Permit | Electrical plans and diagrams |
Plumbing Permit | Plumbing layout and pipe diagrams |
Important: It’s crucial to consult with your local zoning office early in the planning process to avoid any misunderstandings or delays in securing permits for your garage construction.
Choosing the Right Materials for a Robust Business Garage
When building a garage for your business, selecting the appropriate materials is crucial for ensuring long-term durability and functionality. The right choice of materials can help protect your assets, minimize maintenance costs, and ensure that your garage can withstand the demands of daily operations. Whether you plan to store vehicles, equipment, or products, understanding the characteristics of each material will guide you in making the best decision for your needs.
Start by considering the climate, purpose, and load-bearing requirements of the garage. Materials that offer weather resistance, insulation, and structural integrity are paramount. Additionally, balance the upfront cost with long-term savings to ensure you're making a wise investment.
Key Materials to Consider
- Steel – Known for its strength and resistance to weather conditions, steel is a popular choice for the framework and walls of a business garage.
- Concrete – Provides a solid foundation and durability. Concrete floors are essential for heavy traffic and equipment storage.
- Insulation Materials – Options such as foam board or spray foam help maintain temperature control inside the garage.
- Wood – Ideal for certain structural components or aesthetic accents, though it may not provide the same level of protection as steel or concrete.
Considerations for Choosing the Right Materials
- Weather Resistance: Ensure the materials you choose can handle extreme temperatures, rain, or snow.
- Security: Select materials that offer security and protection against unauthorized access.
- Maintenance: Choose low-maintenance materials to reduce upkeep costs and time.
Remember, investing in high-quality materials may have a higher upfront cost but can save you money over time due to fewer repairs and maintenance needs.
Material Cost Comparison
Material | Cost (per sq. ft.) | Durability | Maintenance |
---|---|---|---|
Steel | $5-$10 | High | Low |
Concrete | $3-$6 | Very High | Very Low |
Wood | $4-$8 | Medium | High |
Insulation (Foam) | $2-$4 | Medium | Low |
Designing the Layout for Optimal Workflow and Storage
When planning the layout of a garage for business purposes, it’s crucial to maximize both the operational efficiency and storage capacity. A well-thought-out floor plan not only ensures smooth day-to-day operations but also contributes to long-term organizational success. The layout should facilitate easy movement of personnel and equipment while minimizing obstacles that could hinder workflow.
Key considerations in the design include creating clearly defined zones for different tasks, efficient storage solutions, and pathways for easy access to essential tools or materials. Proper organization of space helps in reducing time spent searching for items and ensures that each task is performed without unnecessary interruptions.
Organizing Functional Zones
- Work Area: Central space for tools, machinery, and vehicles.
- Storage Space: Dedicated areas for materials, parts, and finished products.
- Admin Zone: Office space for paperwork, meetings, and computer work.
Maximizing Storage Efficiency
"Effective storage is essential for keeping the garage organized and accessible. Utilizing vertical space and specialized shelving units can dramatically increase storage capacity."
- Vertical Shelving: Install tall shelves to store materials, tools, and equipment off the floor.
- Modular Racks: Use adjustable racks for flexibility in organizing varying sizes of items.
- Overhead Storage: Consider overhead bins for seasonal or rarely used equipment.
Optimizing Traffic Flow
Area | Recommended Path Width | Notes |
---|---|---|
Work Area | 6-8 feet | Ensure enough space for movement of equipment and personnel. |
Storage Zones | 4-6 feet | Allow access to shelves and bins without overcrowding. |
Vehicle Entry/Exit | 10-12 feet | Wide enough for safe vehicle movement and unloading. |
Hiring Contractors: Key Considerations and Important Questions
When selecting a contractor for your garage construction project, it’s essential to thoroughly assess their qualifications and reliability. The right contractor can help ensure that the project runs smoothly, meets deadlines, and adheres to budget constraints. Focusing on specific skills, experience, and professionalism can save you from costly mistakes and delays down the line.
Here are some key aspects to focus on when evaluating potential contractors for building your garage:
What to Look for in a Contractor
- Licensing and Insurance: Ensure the contractor is licensed to work in your area and has the necessary insurance for both liability and worker's compensation. This protects you from potential legal and financial risks.
- Experience with Similar Projects: Choose a contractor with prior experience building garages or similar structures. A knowledgeable contractor will be familiar with local zoning regulations and common challenges associated with garage construction.
- Reputation and References: Ask for references from past clients. Look for contractors who have a solid reputation for delivering quality work on time and within budget.
- Clear Communication: Effective communication is vital. Make sure the contractor listens to your needs and responds clearly to your questions and concerns.
Questions to Ask a Contractor
- What is your timeline for completion? Make sure the contractor provides a clear and realistic timeline for the project’s start and end dates.
- Can you provide a detailed written estimate? A breakdown of costs, including materials and labor, will help you assess the overall budget and avoid unexpected expenses.
- How do you handle changes or unforeseen issues during construction? Understanding the process for managing scope changes will give you clarity on how flexible and responsive the contractor is.
- Will you pull the necessary permits for this project? Confirm that the contractor is willing and able to handle all legal and regulatory requirements related to construction permits.
Tip: Always request a written contract that outlines the scope of work, timeline, payment schedule, and warranty terms before the project begins.
Contractor Evaluation Table
Criteria | What to Check |
---|---|
Licensing & Insurance | Verify that the contractor holds the appropriate licenses and insurance for the job. |
Experience | Look for contractors with experience in garage construction or similar projects. |
References | Ask for at least 2-3 references to gauge the contractor's past performance. |
Communication | Assess how well the contractor communicates with you during initial discussions. |
Creating a Budget for Your Garage Construction Project
When planning the construction of a garage for your business, one of the first steps is determining how much you are willing to invest. Proper budgeting ensures that you don't face unexpected financial strain as the project progresses. It's essential to break down your expenses and plan ahead for every stage of construction.
To ensure you stay within budget, you'll need to account for several key expenses. These include land preparation, materials, labor, permits, and potential unforeseen costs. Below are the critical components to consider when estimating your garage construction budget.
Key Cost Categories
- Land Preparation: This includes grading, clearing, and leveling the site for construction.
- Materials: You will need to budget for concrete, steel, wood, insulation, and other construction materials.
- Labor: Skilled workers, including contractors, electricians, and plumbers, will contribute to a significant portion of the budget.
- Permits and Regulations: Don't forget to factor in the costs of permits, inspections, and any necessary legal compliance.
- Contingency Fund: It's essential to allocate an additional 10-15% of your total budget for unforeseen costs.
Steps to Estimate Construction Costs
- Assess the Size: Determine the dimensions and design of the garage based on your business needs.
- Get Multiple Quotes: Request quotes from different contractors and suppliers to ensure competitive pricing.
- Account for Site Specifics: If the land requires significant grading or preparation, this will impact your overall cost.
- Incorporate a Contingency: Set aside a percentage of the budget for unexpected issues that may arise during construction.
Tip: Always overestimate your costs slightly rather than underestimating them. This cushion will help you avoid budgetary surprises.
Sample Budget Breakdown
Item | Estimated Cost |
---|---|
Land Preparation | $5,000 |
Materials | $15,000 |
Labor | $10,000 |
Permits and Inspections | $2,500 |
Contingency Fund (10%) | $3,200 |
Total Estimated Cost | $35,700 |
Maintaining Your Garage After Construction Completion
Once the construction of your garage is complete, the focus should shift to ensuring its longevity and functionality. Proper upkeep is essential to avoid costly repairs and to keep the space in optimal condition for your business operations. Regular inspections, cleaning, and minor repairs can make a significant difference in maintaining the garage’s structure and equipment.
To effectively manage the garage, it is important to implement a routine maintenance schedule. This will help identify potential issues before they escalate. Below are key practices to keep your garage running smoothly after construction:
Routine Inspections and Cleaning
Regular inspections allow you to identify small issues early, saving time and money on future repairs. Cleaning the garage is equally important, as dust and dirt can accumulate and affect both the structural integrity and the equipment within. Focus on:
- Checking the roof and walls for leaks or cracks.
- Inspecting doors and windows for proper sealing.
- Ensuring that the electrical and plumbing systems are functioning properly.
Preventive Maintenance for Equipment
Keeping your garage equipment in good working order is crucial for minimizing downtime. Follow these guidelines:
- Lubricate moving parts on garage doors and machinery regularly.
- Test lighting and electrical circuits to ensure they meet operational needs.
- Perform seasonal checks on heating and cooling systems if applicable.
Tip: Keep a log of all inspections and repairs to track maintenance over time.
Common Maintenance Checklist
Task | Frequency | Action |
---|---|---|
Roof Inspection | Annually | Look for leaks, damage, or debris. |
Garage Door Functionality | Quarterly | Check for smooth operation and lubricate moving parts. |
Electrical System Check | Every 6 months | Ensure all circuits are working and no wiring is exposed. |