How to Produce Garage
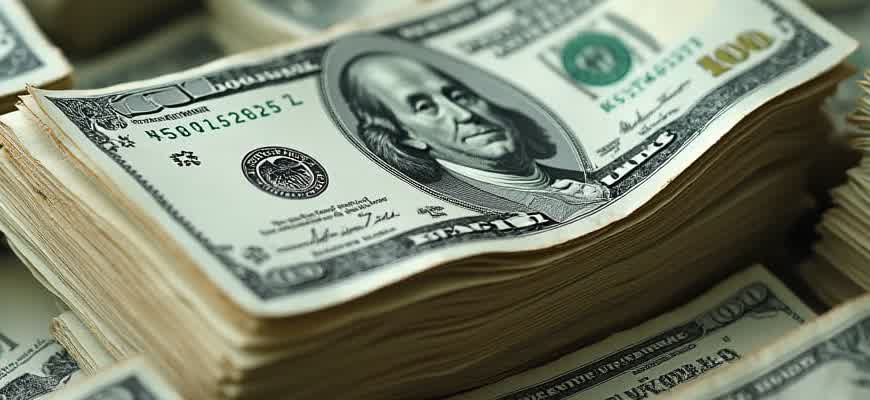
Building a garage requires careful planning and the right materials. The following sections provide an overview of the key steps involved in the process.
- Planning the Design: Before starting, determine the purpose of the garage. Will it be used for parking, storage, or as a workshop?
- Choosing the Location: The site for the garage should be level and easily accessible, with enough space for the building and any vehicles.
- Gathering Materials: Select durable materials that can withstand the local climate. Common choices include wood, steel, or concrete.
The following table summarizes common building materials and their advantages:
Material | Advantages |
---|---|
Wood | Cost-effective, easy to work with |
Steel | Strong, low maintenance |
Concrete | Durable, fire-resistant |
It's crucial to ensure that the garage is built according to local building codes and regulations. Always consult with a professional if you're unsure about legal requirements.
Choosing the Right Location for Your Garage Production
When setting up a production space for your garage music project, selecting the optimal location is crucial for both technical and practical reasons. A well-chosen environment will ensure minimal disruptions, good acoustics, and efficient workflow. The location should meet your equipment needs while also offering a comfortable, sound-friendly atmosphere for long sessions. It's important to consider factors such as noise, space, accessibility, and overall vibe.
Choosing the right spot within your home or studio should be done with careful thought. Noise control, space for expansion, and availability of power sources are just some of the key aspects to consider. Additionally, the location must allow easy access to instruments, recording gear, and other essential components of the production process. Here's how to evaluate the best space for your needs:
Key Factors to Consider
- Acoustics: Sound quality can be affected by room shape, size, and materials used. A room with reflective surfaces may cause unwanted echoes, while a carpeted space could help dampen the sound.
- Noise Isolation: Ensure the room is away from external noise, such as street sounds or household activity. Soundproofing materials can also be used to reduce interference.
- Space and Layout: A spacious room will allow you to set up your equipment comfortably and move around freely. Consider the room's layout for optimal gear placement and workflow.
How to Find the Best Location
- Start with Quiet Areas: Choose a space that is as isolated as possible from high-traffic zones in your home.
- Test Room Acoustics: Walk around the room and listen for echoes or unwanted reverb. Consider soundproofing or acoustic treatment if necessary.
- Assess Power Supply: Check for adequate power outlets and the possibility of running additional cables without disruptions.
"The room you choose should align with the nature of the music you're creating, whether it demands a dry, controlled sound or a more live, ambient feel."
Room Size vs. Production Needs
Room Size | Best For |
---|---|
Small (Up to 100 sq ft) | Solo productions, minimal gear setups, small recording sessions. |
Medium (100-200 sq ft) | Small bands, larger instrument setups, flexible layouts. |
Large (200 sq ft and above) | Full band setups, multiple instruments, soundproofed isolation booths. |
Designing a Functional Garage Layout for Maximum Efficiency
Optimizing the space in a garage is essential for creating a workspace that supports productivity and ease of access. Proper planning ensures that tools, equipment, and vehicles are positioned to enhance workflow while minimizing unnecessary movement. A well-thought-out layout also helps to maintain organization, reduce clutter, and ensure safety when using various garage tools.
When designing the layout, the focus should be on clear zoning, efficient storage, and accessibility. Keeping these principles in mind will allow you to fully utilize the garage’s square footage while maintaining a smooth operational flow. Below are some key factors to consider when creating a functional garage setup.
Key Factors for an Efficient Garage Layout
- Workflow Zones: Divide the garage into functional areas such as a workbench zone, storage area, and vehicle parking zone.
- Vertical Storage: Use wall-mounted shelves, pegboards, and overhead racks to maximize vertical space and keep the floor clear.
- Clear Access Paths: Ensure that each zone has enough space for easy movement, and tools or vehicles can be accessed quickly.
- Lighting and Ventilation: Good lighting and air circulation are essential for safety and efficiency, especially in work areas.
Optimizing Garage Workflow
To ensure that your garage remains efficient, create a logical flow of movement. For example, position the workbench near the storage for tools but away from parked vehicles. Consider the following layout tips:
- Workbench Area: Keep the workbench against a wall to allow easy access to tools and materials while ensuring that it's well-lit.
- Vehicle Parking: Reserve the back half of the garage for vehicle storage, leaving enough room to open doors and access the trunk or hood.
- Storage Solutions: Use cabinets and drawers to store small tools, keeping them off the workbench, and install overhead racks for larger items like ladders or sporting equipment.
"Efficient garage design maximizes the use of every inch of space while ensuring that everything has its place and is easily accessible."
Sample Garage Layout
Zone | Recommended Features |
---|---|
Workbench Area | Wall-mounted shelves, adjustable lighting, easy access to hand tools |
Vehicle Storage | Clear path for vehicle entry/exit, ample space for door opening |
Tool Storage | Wall pegboards, tool cabinets, labeled drawers |
General Storage | Overhead racks, corner shelving, stackable bins |
Essential Tools and Equipment Needed for Garage Production
When setting up a space for producing garage music, it is crucial to have the right tools and equipment. From sound sources to mixing gear, each component plays a significant role in shaping your tracks. This list covers everything you need to ensure smooth production in a home studio or garage setup.
Whether you're just starting or looking to upgrade your setup, certain items are indispensable. With the proper gear, you can enhance both the creative and technical aspects of your work. Below is a list of essential tools that will support various stages of the music production process.
Key Equipment for Garage Music Production
- Audio Interface: This device allows your computer to communicate with audio sources like microphones and instruments. Look for an interface with at least two inputs and outputs for versatility.
- Studio Monitors: High-quality speakers are essential for accurately hearing your mixes. Opt for monitors that provide flat frequency response.
- Microphones: Depending on your production style, dynamic or condenser mics will help capture vocals or instruments effectively.
- MIDI Controller: A keyboard or pad controller is crucial for programming beats and melodies with ease.
- Headphones: A pair of closed-back headphones for tracking and open-back for mixing will cover different needs.
- Acoustic Treatment: Improve the sound of your space with bass traps and foam panels to reduce unwanted reflections.
Other Helpful Tools and Accessories
- DAW (Digital Audio Workstation): A powerful software tool to record, edit, and arrange your music. Popular choices include Ableton Live, FL Studio, and Logic Pro X.
- VST Plugins: Virtual instruments and effects that expand the range of sounds available for production.
- Cables and Stands: Reliable cables (XLR, TRS, etc.) are essential, along with mic stands and speaker stands to keep your setup organized.
- External Hard Drive: An extra storage solution to keep your projects safe and organized.
Important Considerations
For maximum productivity, ensure that your studio environment is well-organized. A clutter-free workspace will allow for greater focus and creativity.
Quick Overview of Equipment Setup
Equipment | Purpose |
---|---|
Audio Interface | Connects microphones, instruments, and other devices to your computer |
Studio Monitors | Provides accurate sound reproduction for mixing |
Microphone | Captures audio for vocals and instruments |
MIDI Controller | Allows for easier control of virtual instruments and beats |
DAW | Software for arranging and editing your music |
Setting Up a Production Line in Your Garage Space
Transforming your garage into a fully functional production space requires careful planning and organization. The limited space available means you'll need to be strategic about equipment placement, workflow, and soundproofing. Additionally, the equipment you choose will largely depend on the style of music you're aiming to produce. Whether it's electronic beats or lo-fi sounds, setting up a dedicated and efficient work environment is key.
First, consider the layout of your garage and make sure to clear any unnecessary items. This will give you a blank canvas to work with. Next, think about power requirements, acoustics, and ventilation. A proper setup ensures that your work is both efficient and conducive to creativity.
Key Elements to Consider When Setting Up Your Garage Production Space
- Acoustic Treatment: Proper soundproofing and room treatment are essential to prevent unwanted noise interference and to get accurate mixes.
- Electrical Setup: Ensure that your space has enough outlets to handle all your equipment, such as synthesizers, computers, and audio interfaces.
- Lighting: Bright and adjustable lighting can reduce eye strain and help maintain focus during long production sessions.
Necessary Equipment for Garage Music Production
- Audio Interface: Allows you to connect instruments, microphones, and speakers to your computer.
- Monitors: High-quality speakers will help you hear your mixes accurately.
- DAW (Digital Audio Workstation): Essential software for composing, mixing, and producing music.
- Microphones and Headphones: For recording vocals and getting clear feedback during the production process.
- Keyboard or MIDI Controller: Useful for creating melodies and beats directly into your DAW.
Sample Layout for Garage Music Studio
Area | Purpose |
---|---|
Desk | Positioned centrally for easy access to computer, audio interface, and DAW controls. |
Monitors | Placed on either side of the desk, at ear level for optimal sound accuracy. |
Instruments | Should be stored in an easily accessible place, away from the desk but within arm's reach. |
Acoustic Treatment | Strategically placed foam panels and bass traps to minimize unwanted reverberation. |
Tip: Keep cables organized and avoid cluttering the space. Use cable management tools to ensure safety and ease of access.
Managing Material Supply and Inventory in a Garage Setup
Efficient material management is a cornerstone of any well-functioning garage operation. From tools and parts to consumables like lubricants and cleaning supplies, maintaining a streamlined inventory ensures a smooth workflow and minimizes downtime. Having a clear system in place can greatly enhance both productivity and cost-effectiveness, allowing a garage to operate without disruptions due to supply shortages or overstocking.
One of the first steps in creating an effective inventory system is identifying essential materials. This includes everything from replacement parts for vehicles, basic repair tools, and specialty equipment, to maintenance supplies like oils, filters, and batteries. Categorizing these items into high-demand, seasonal, or occasional use can help prioritize storage and purchasing decisions.
Key Aspects of Material Management
- Inventory Tracking: Use digital tools or spreadsheets to monitor the quantity and condition of stock items regularly. Setting up automated alerts for low stock levels can prevent sudden shortages.
- Storage Organization: Proper organization of the storage space ensures quick access to tools and parts. Shelving, drawers, and labeled containers can significantly reduce the time spent searching for materials.
- Supplier Relationships: Building strong connections with reliable suppliers ensures the availability of materials on demand, and it can also lead to better pricing or faster delivery times.
Optimizing Stock Levels
- Analyze Usage Patterns: Review consumption rates to determine reorder points. For example, if certain parts or consumables are used frequently, keep a larger stock of those items.
- Avoid Overstocking: Over-purchasing can lead to unnecessary capital tied up in inventory. Balance between having enough stock to meet demand without overloading storage space.
- Regular Audits: Conduct routine stock checks to ensure that materials are properly accounted for and that no items are damaged or expired.
"A well-managed inventory system not only keeps the garage running efficiently but also saves money in the long run by minimizing waste and optimizing material purchases."
Example of Inventory Categories
Category | Items Included | Frequency of Use |
---|---|---|
Tools | Wrenches, Screwdrivers, Hammers | High |
Vehicle Parts | Brake Pads, Oil Filters, Belts | Medium |
Consumables | Lubricants, Cleaning Products, Adhesives | High |
Specialty Equipment | Diagnostic Tools, Welding Machines | Low |
Managing Noise and Ensuring Safety in a Garage Studio
In a home or DIY garage studio, managing noise and ensuring the safety of the space are critical to both the quality of work and the well-being of those involved. Soundproofing techniques and awareness of potential hazards can help create a more comfortable and secure environment for music production or any workshop-related activity. Failure to address these issues may lead to distractions or even serious accidents. Below are essential steps to reduce unwanted noise and enhance safety within the garage workspace.
Noise control in a garage setting can be particularly challenging due to its structural properties. The space often lacks sound isolation, which can result in sound leakage, affecting both the producer and the surrounding neighborhood. Moreover, the risk of injury is heightened by tools, equipment, and clutter. It's important to be proactive in creating a safer and quieter environment.
Noise Reduction Techniques
- Soundproofing the Walls: Adding soundproof materials such as foam panels or mass-loaded vinyl to walls and ceilings can significantly reduce sound leakage.
- Sealing Gaps: Ensure that doors and windows are sealed properly to minimize sound transmission. Use weatherstripping or acoustic seals around openings.
- Floor Treatment: Rugs or carpets can help reduce sound bouncing off hard surfaces, which can contribute to unwanted echoes.
- Isolation Pads for Equipment: Using isolation pads under speakers, amplifiers, and other loud equipment helps absorb vibrations and minimizes sound transfer through floors.
Safety Measures
Safety should always be a priority in a garage environment where heavy equipment, power tools, and other hazards are prevalent. Setting up a clear and organized workspace is the first step toward reducing risks.
- Proper Tool Maintenance: Always keep tools in good condition. Regularly check for wear and tear, ensuring all equipment is functional and safe to use.
- Protective Gear: Wear safety equipment such as goggles, ear protection, and gloves when handling machinery or power tools.
- Clear Workspace: Keep the garage tidy and free of clutter to reduce the risk of trips, falls, and accidents.
It is essential to follow proper safety protocols and create a noise-conscious environment to ensure both your health and the quality of your work in a garage studio.
Emergency Safety Checklist
Safety Measure | Details |
---|---|
First Aid Kit | Ensure a well-stocked first aid kit is easily accessible in case of accidents. |
Fire Extinguisher | Install a fire extinguisher close to any heat-producing equipment or materials. |
Clear Exit Routes | Make sure exits are unobstructed for quick evacuation in emergencies. |
Optimizing Workflow to Increase Output in a Limited Space
Efficient use of space is critical when working in environments with physical constraints. A well-organized workflow can significantly enhance productivity, even in compact settings. In particular, a strategic layout and streamlined processes help maximize output without unnecessary waste of time or resources. The goal is to create a system that minimizes movement, reduces clutter, and allows for easy access to tools and materials, ensuring a smooth, uninterrupted work process.
Adopting a systematic approach to task management and workspace design can also boost efficiency. In a confined space, every inch counts. By analyzing the most common tasks and tools used, you can optimize the flow and ensure that everything is within arm’s reach when needed. This approach requires careful planning and periodic adjustments to accommodate changing workflows or tasks.
Key Steps to Streamline Workflow
- Space Evaluation: Analyze the available space and identify areas where you can introduce organizational systems. Ensure that the most frequently used items are within easy reach, and less-used tools are stored away but still accessible.
- Process Standardization: Standardize your methods for tasks to reduce decision fatigue and wasted effort. This includes creating consistent routines for tool usage, material handling, and cleaning.
- Use of Vertical Space: Utilize wall-mounted storage and shelves to free up floor space. This can help reduce clutter and allow for easy access to supplies.
Efficient Tool and Material Handling
- Tool Placement: Place tools in locations based on their frequency of use. Items used often should be placed in easily accessible positions, while items used infrequently can be stored in less accessible locations.
- Material Organization: Group materials by type and usage frequency. Consider using labeled bins or containers to quickly identify what’s needed.
- Workstation Layout: Set up workstations that cater to specific tasks, minimizing movement between areas and keeping tools and materials in close proximity.
Tip: Periodically assess your workspace to identify opportunities for improvement. Small changes, like moving a frequently used tool closer or rearranging a workstation layout, can result in significant time savings.
Comparison of Layout Options
Layout Type | Advantages | Challenges |
---|---|---|
Linear Layout | Simple, easy to follow, reduces unnecessary movement. | Can be limited by available space, may require more steps to access tools in a narrow environment. |
Circular Layout | Allows for more flexible movement and easy access to tools. | Can lead to clutter if not carefully organized, may require more space. |
Modular Layout | Highly customizable and adaptable to changing tasks. | Requires frequent adjustments and reorganization based on evolving needs. |